Continuous conveyor ovens are widely used in a variety of industrial processes including composite curing and heat treating. The entrance and exit points of these ovens represent significant areas for potential heat loss and energy inefficiencies. Without a proper heat barrier system these openings can be the culprit for thousands of dollars in wasted energy cost. In addition, regulating and controlling critical process temperatures can become a daunting task with inadequate heat containment.
Utilizing Worbo’s unique high temperature strip curtain system, energy costs may be significantly reduced and process temperatures may be accurately controlled. These strip curtains serve as an effective thermal barrier while allowing for the passage of parts through the oven chamber. Unlike traditional PVC strips that will break down at moderate temperatures the Worbo solution can withstand excessive temperatures and will continue to function effectively up to 1000oF.
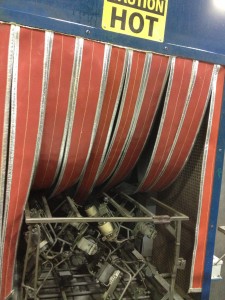
A typical example of a proven and extremely effective Worbo strip curtain design consists of a double layer heat barrier system. In this system the inside face of each strip if fabricated from Worbo’s exceptional Eko-ThermTM heat reflective material. This unique material serves to retain convective heat with in the oven chamber in addition to preventing radiant heat from escaping through the oven door. The outside face of each strip is fabricated from Worbo’s extreme duty MSA96 (96 oz/yd2) silicone coated fabric offering outstanding durability and abrasion resistance as moving parts are transferred though the oven opening.
![]() |
![]() |
In addition to generating significant energy cost savings, Worbo’s high temperature strip curtains offer the following key benefits:
- Reduce the risk of workplace burn hazards near the opening of the oven.
- Strips are easy to install and individual strips are simple to replace should they become damaged without the need to replace the entire curtain.
- Excellent abrasion resistance and exhibit outstanding durability as parts move in and out of a conveyor oven.
- Allows for oven temperatures to be accurately controlled ensuring product consistency and quality is upheld.
- Manufacturing cycles are increased as the thermal barrier facilitates faster oven pre-heat time.
- Strip curtains may be supplied in a variety of widths and lengths to custom fit virtually any oven opening.
Worbo’s heat resistant strip curtains are tailor made for each specific application in consideration of temperature constraints, environmental conditions, cycle frequency, oven geometry, etc. Contact the design team at Worbo to assist with your continuous conveyor oven application.